Considerações ao montar uma solda a ponto a partir de um transformador de micro-ondas.
Antes de continuar, para quem não sabe o que é um aparelho de solda a ponto, dá uma lida nesse artigo -> aqui <- que está bem interessante e depois continue aqui para ver o que precisa se levar em conta quando prototipando um aparelho de solda a ponto :-).
Se você curtir esse artigo, não esqueça de dar uns cliques nos anúncios para ver o que os anunciantes tem para te oferecer. Vou ficar muito contente.
Como tudo começou:
Há um tempinho atrás, eu estava pesquisando nos sites de comércio eletrônico da China, o preço e como são as máquinas de solda a ponto, daquelas para montar packs de baterias que nem a da figura 1 abaixo:
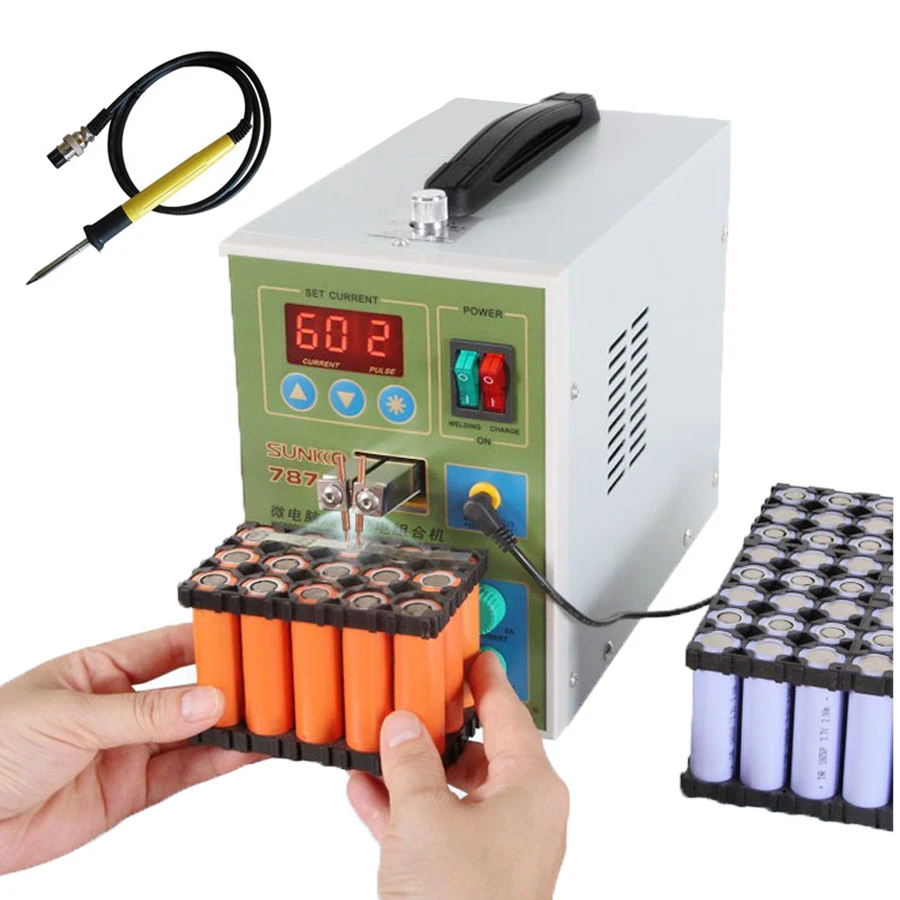
Nessa onda de ir pesquisando, quando ordenei o preço das máquinas de solda a ponto das mais em conta para as mais caras, acabei descobrindo que é possível comprar e comprei, somente as placas de controle do equipamento de solda, que são as plaquinhas vermelhas da figura 2 abaixo, ficando por conta do comprador a aquisição dos demais componentes e a montagem final do aparelho.
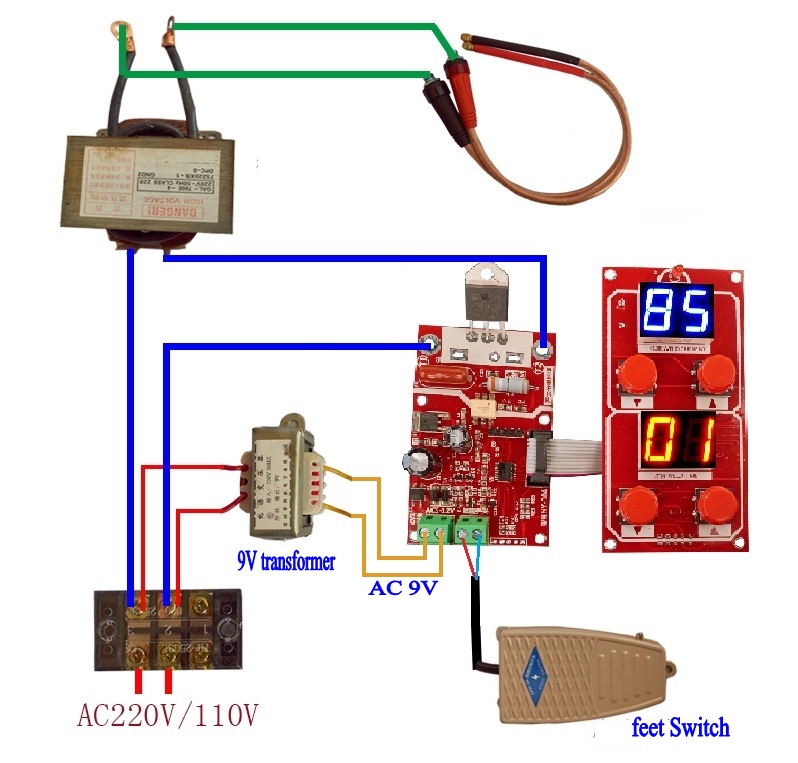
E o preço, é mais barato?
Não. Prototipar, mesmo que seja apenas a montagem de um gabinete, nunca é mais barato que comprar algo pronto a menos que seja uma aplicação extremamente específica.
Embora eu sempre tenha um olho aberto para um eventual estudo de viabilidade, tenho consciência que é muito mais caro desenvolver um produto completo do que comprar um que esteja na prateleira.
O negócio aqui é mais pela diversão, o passa tempo, o gostinho de montar algo com as próprias mãos, que no final das contas terá alguma utilidade.
Trata-se de um quebra cabeças sem manual.
Com as plaquinhas em mãos da figura 3 abaixo, começa a montagem do quebra cabeça, que é definir qual caixa será utilizada, fiação e todos os detalhes de se transformar uma promessa em uma ferramenta.
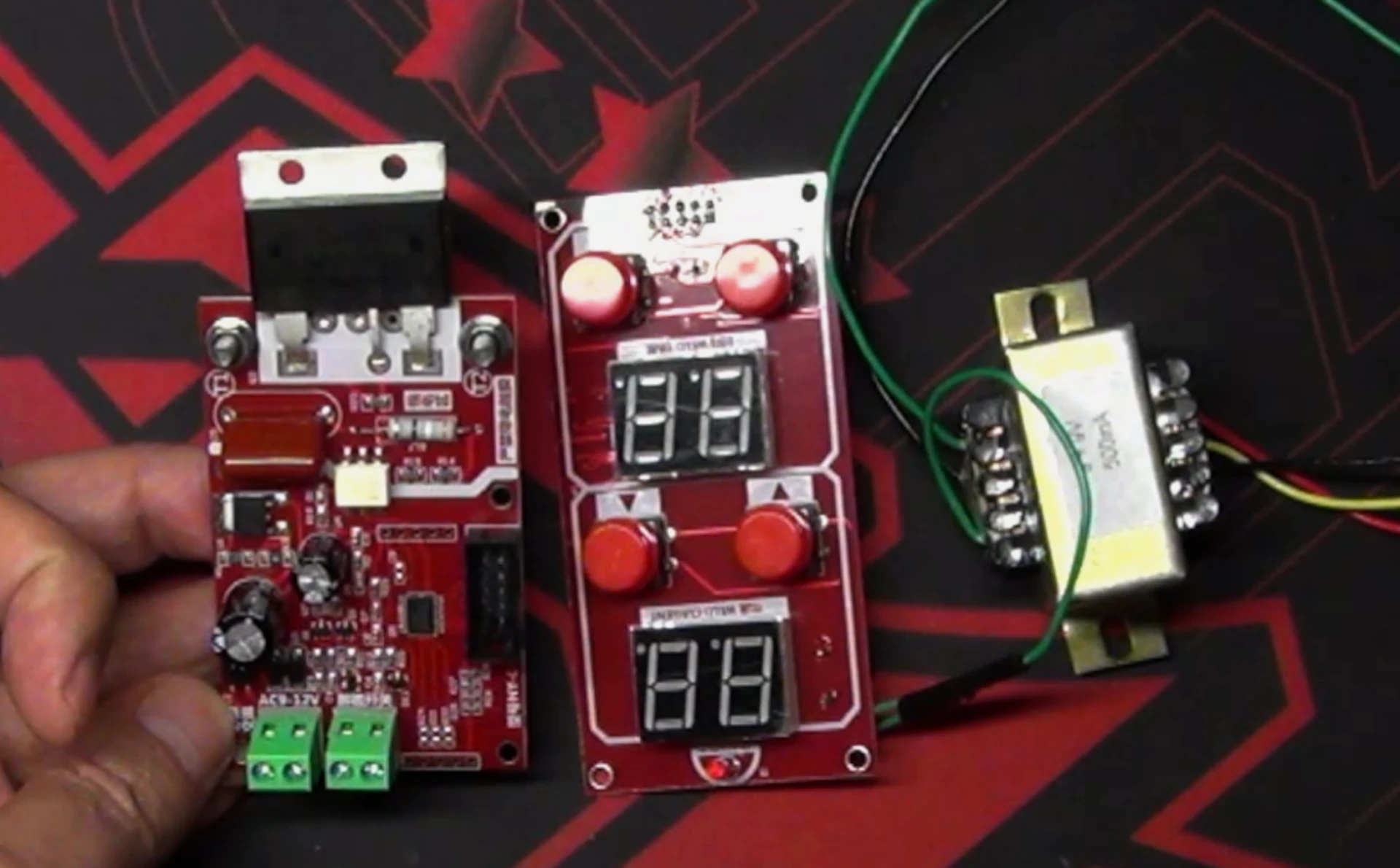
Definida a plaquinha, o que mais?
Precisa:
- Arrumar os componentes que faltam,
- Definir a caixa para colocar o circuito dentro,
- Arrumar um transformador de micro-ondas,
- Montar o equipamento dentro da caixa,
- E fazer o aparelho funcionar.
Componentes que faltam:
Foi relativamente simples. Um transformador, uns botões liga/desliga e um par de transformadores.
Definir a caixa:
Definir a caixa, nessa montagem foi um caso à parte.
Como esse aparelho utiliza um transformador de micro-ondas, que é relativamente pesado, a caixa precisa ser robusta e barata, coisas que não combinam muito bem.
Depois de muito pesquisar e como eu não tinha nenhum equipamento velho para aproveitar seu gabinete, conforme figura 4, optei por comprar uma caixa de MDF, fazer as furações necessárias e a pintar com tinta spray.
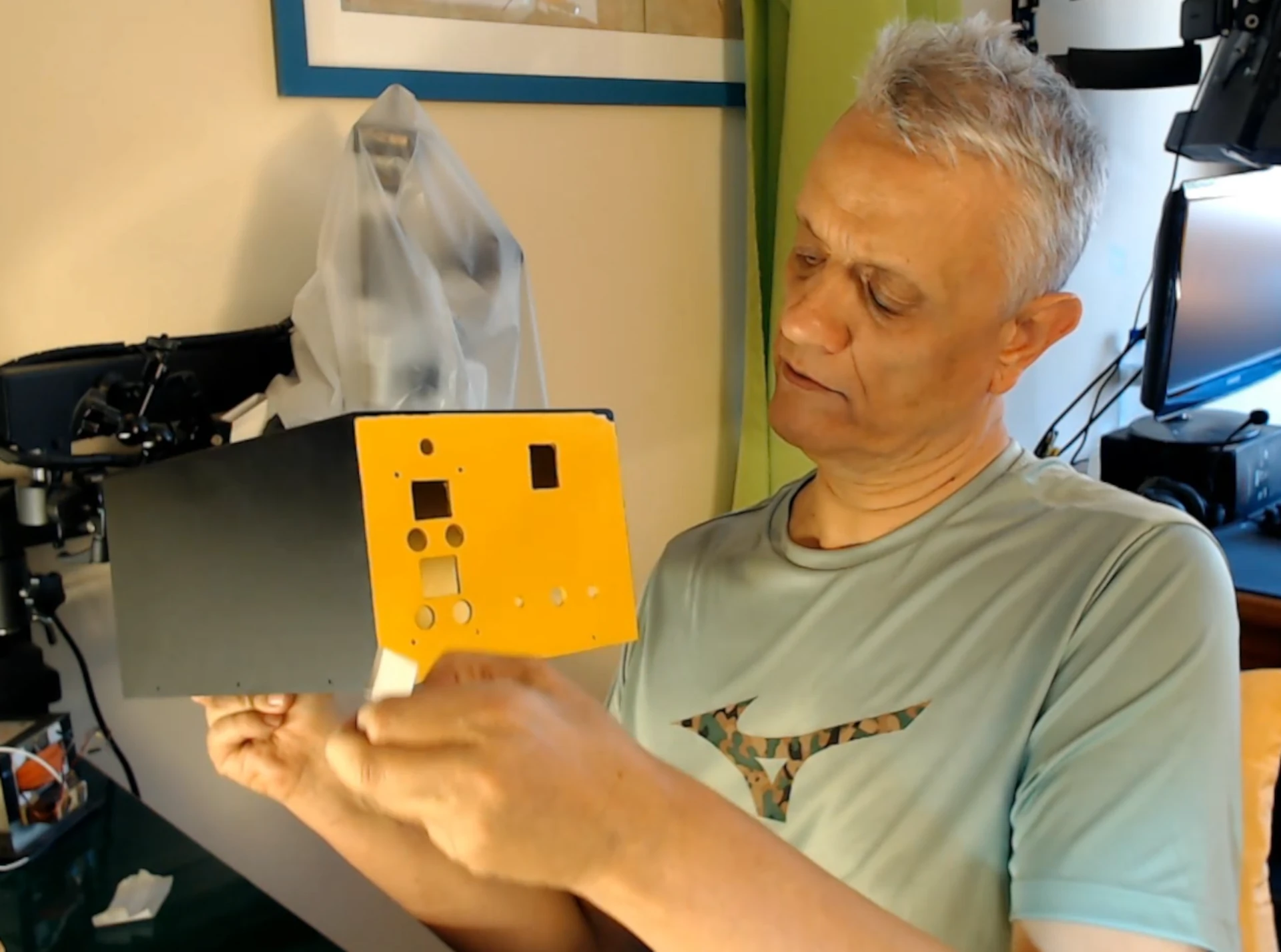
A montagem da caixa em si não teve grandes mistérios, exceto o visor de acrílico dos displays de tempo e potência do equipamento.
Os displays indicadores de tempo e potência devem ter uma janela de acrílico vermelha que encaixe perfeitamente no painel. Isso simplesmente não existe. Tive que projetar no FreeCad e depois tive de usinar no CNC, conforme figura 5 abaixo:
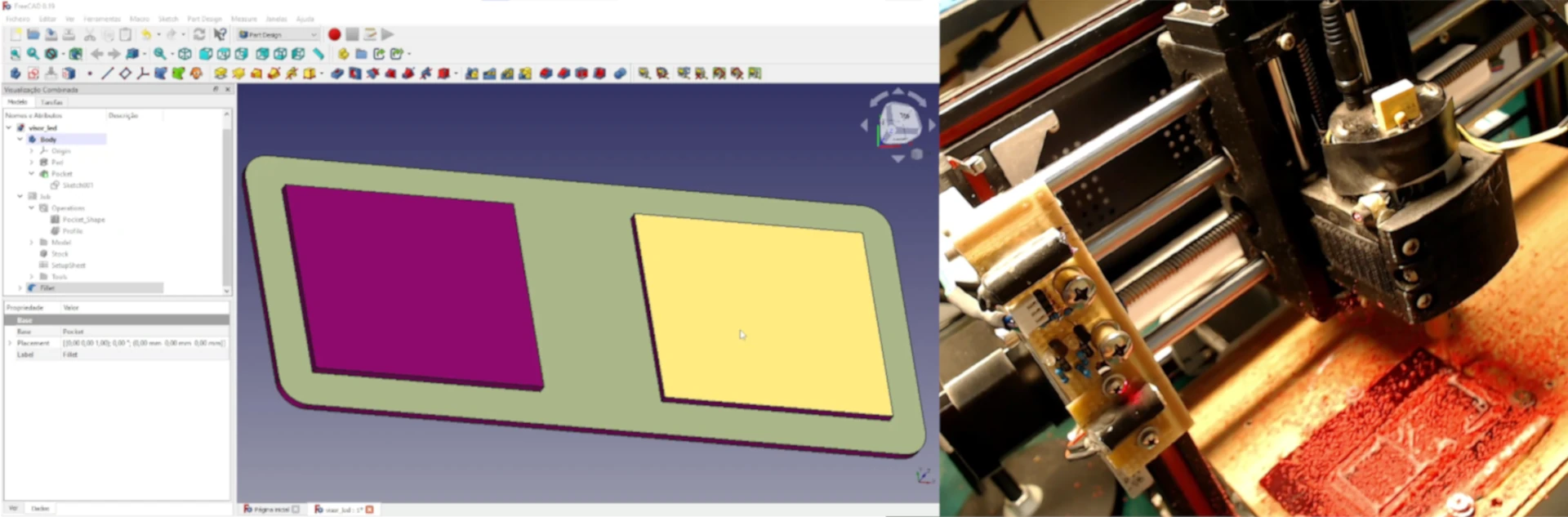
Arrumar um transformador de micro-ondas:
Essa foi fácil. Dei um jeito de arrumar um forno de micro-ondas velhinho, prestes a ser descartado e desmontei seu secundário conforme vou contar adiante.
Montar o equipamento dentro da caixa:
Na hora de montar o equipamento, precisa arrumar espaçadores, pezinhos e o que não tem, a exemplo dos displays, precisa fabricar.
Nessa parte de fabricar peças, nas figuras 6 a 10, para ilustrar o que estou falando, temos a criação do suporte da placa principal.
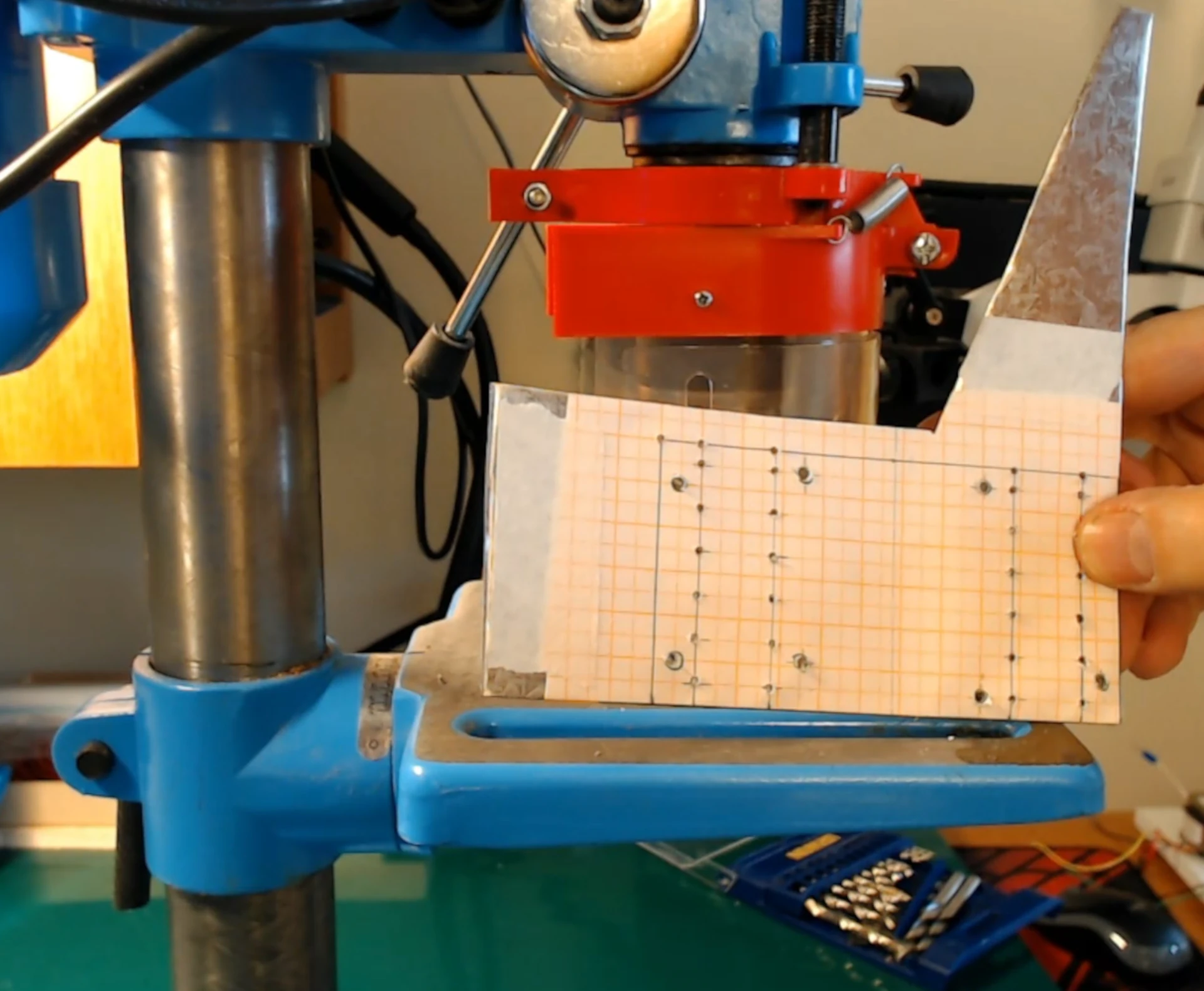
Para criar o suporte, conforme figura 6, precisa fazer uma série de medições, planejar as dobras e furações e montar um modelo..
Muitas vezes, montar esse modelo no papel milimetrado e passar o desenho direto para uma chapa, é muito mais rápido e prático do que fazer um desenho no CAD.
Note que o desenho tem vários furos “desnecessários”. Mais adiante vou explicar para que eles servem.
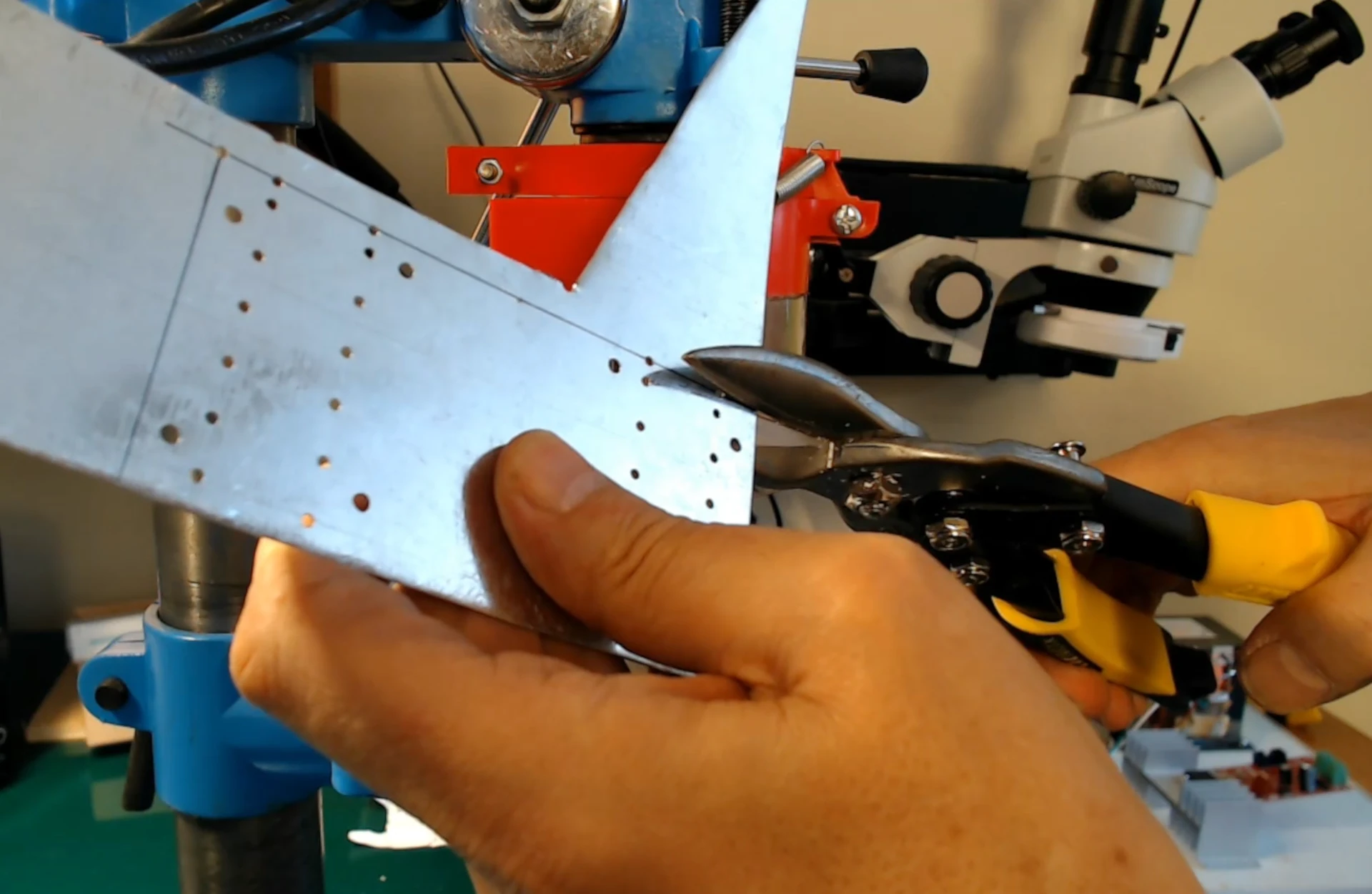
Feitas as furações e rebarbas removidas na lima, basta fazer o corte com uma tesoura de chapa, conforme indicado na figura 7 acima.
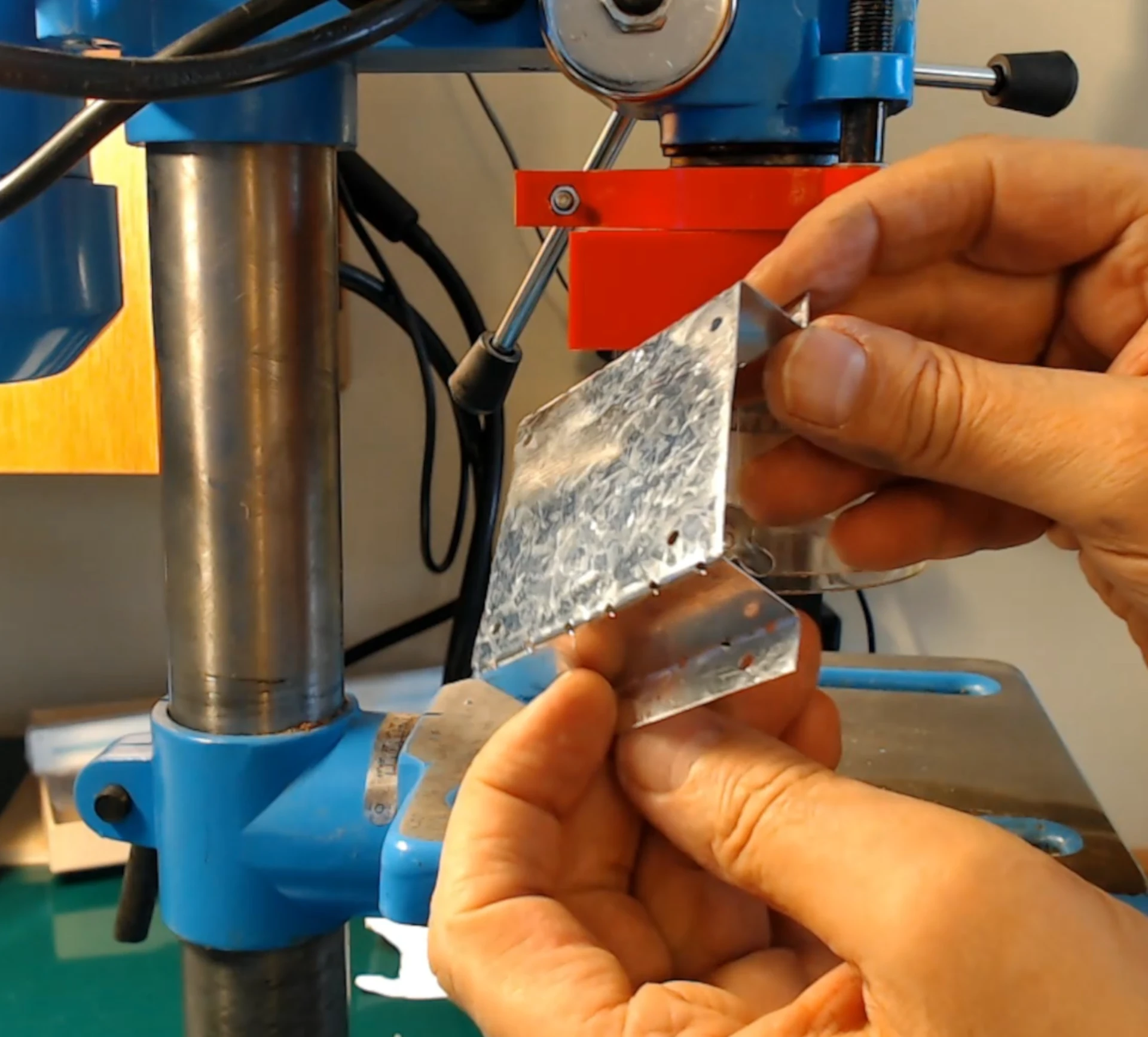
Na figura 8 temos o suporte pronto, depois de dobrado. Lembra daqueles furinhos “desnecessários”?
Então, eles funcionam como uma guia na hora de fazer as dobras da chapa. Usando essa técnica, dá para fazer dobras razoavelmente precisas sem utilizar uma dobradeira. Basta um alicate, um martelo e um pouquinho de persistência.
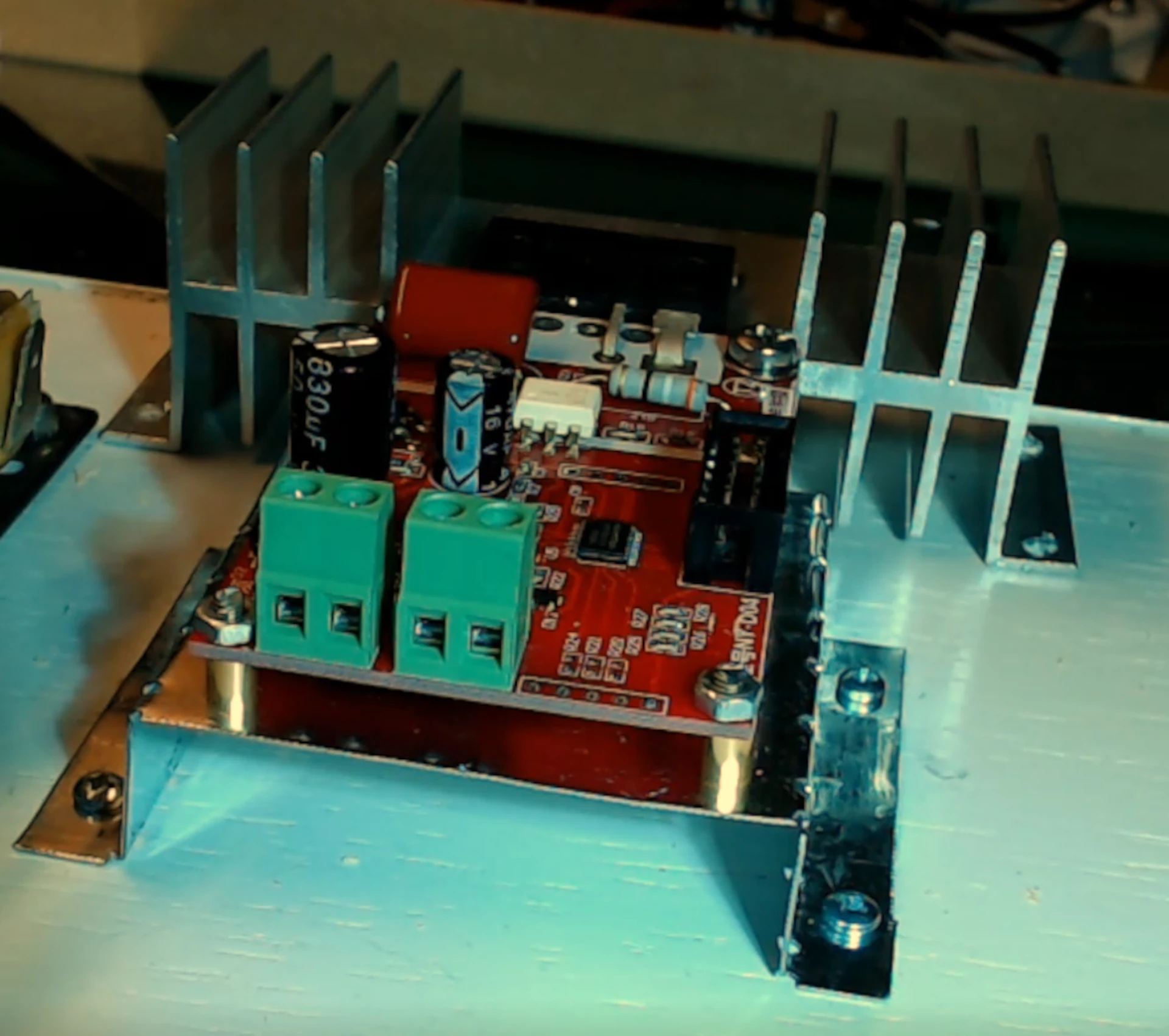
Concluído o suporte, é hora de fixar a plaquinha no suporte.
Aqui temos mais um segredo que é o seguinte: Você está vendo na figura 9 aqueles espaçadores cilíndricos de latão, amarelos?
Então, aqueles espaçadores são peças de bijuteria para montagem de colares.
Muitos dos acabamentos, espaçadores, arruelinhas e isolantes “especiais” e difíceis de achar, a gente encontra em lojas que vendem insumos para fábricas de bijuterias.
Nessa dica, recomendo que você visite as lojas da Ladeira Porto Geral em S. Paulo SP, especializadas em vender materiais para confecção de bijuterias. Tem muita coisa boa para prototipagem por lá ;-).
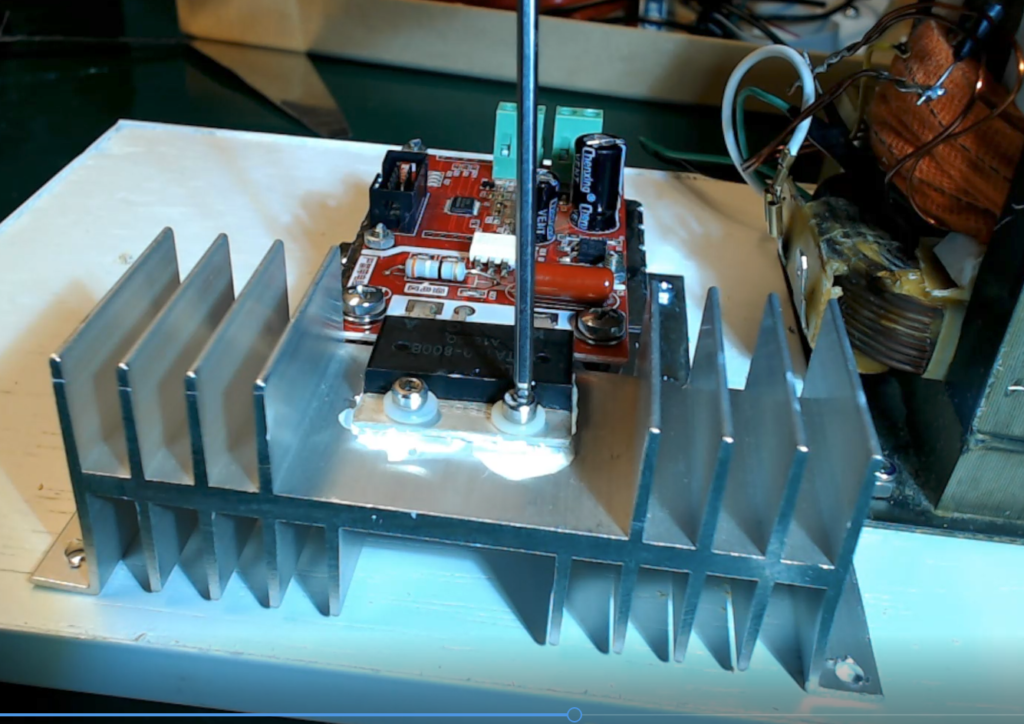
Agora, na figura 10, vem a furação do dissipador de calor que é de alumínio.
Para furar alumínio, tem as seguintes dicas:
- Sempre que der, utilize uma furadeira de bancada, pois ela é muito mais precisa que uma furadeira manual.
- Para furar alumínio, utilize rotação baixa, em torno de 200 a 300rpm.
- Para evitar superaquecimento, aplique pouca pressão na peça.
- Mantenha a peça refrigerada, aplicando álcool ou outro refrigerante enquanto estiver furando.
- Se não tiver broca de cobalto que tem uma melhor dissipação térmica, pode utilizar broca de aço rápido, desde que esteja afiada.
Ainda conforme a figura 10, terminada a furação do dissipador de calor, é hora de montar o IGBT no mesmo.
Nessa etapa precisa atentar para colocar as arruelas isolantes, o espaçador de mica e a pasta térmica, garantindo que o dissipador de calor fique sem nenhum contato elétrico com o IGBT.
Monta-se os demais componentes e fecha-se a caixa, conforme indicado na figura 11 abaixo.
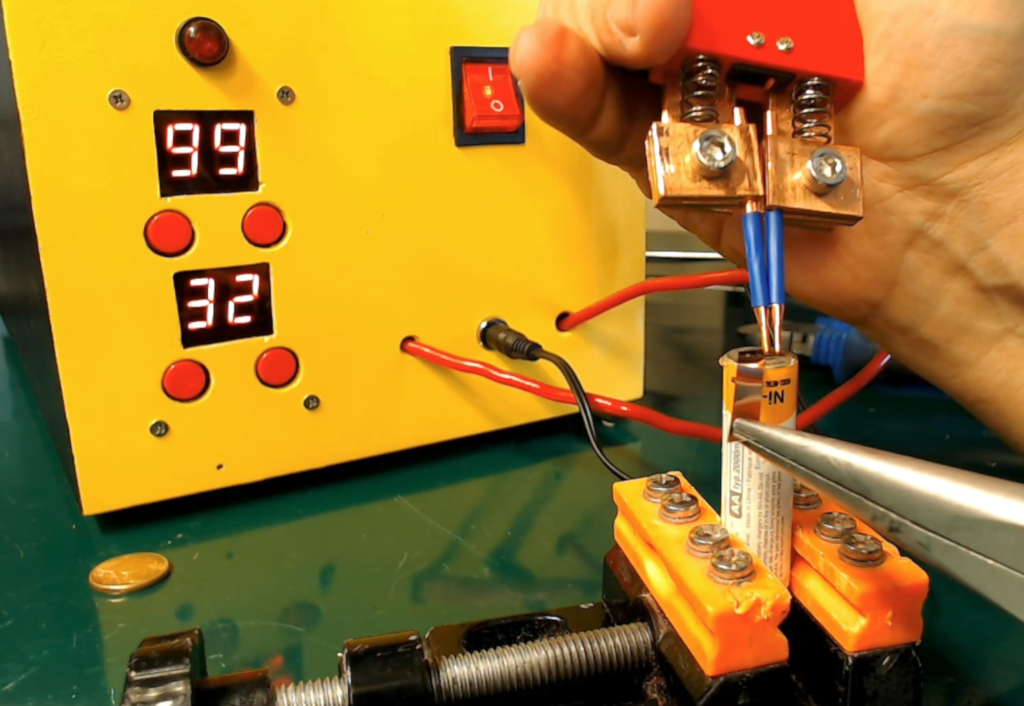
Fazer o aparelho funcionar:
Fazer funcionar essa solda à ponto foi uma parte bem desafiadora.
Tem vários vídeos na Internet mostrando como se faz esse tipo de montagem, mas nenhum deles abordam os perrengues da montagem, principalmente quanto ao enrolamento secundário do transformador.
Isso que é difícil de se fazer:
Embora conseguir fazer o aparelho soldar seja relativamente fácil, o problema é conseguir extrair o máximo possível de potência do transformador.
Sendo mais preciso, não adianta ter potência suficiente para abrir buracos quando soldando chapas finas e faltar potência para soldar áreas maiores, sem danificar componentes internos da bateria, como por exemplo quando soldando o terminal negativo de uma bateria.
A potência do transformador é influenciada pelo modo que o secundário do transformador é enrolado e devo lembrar que a melhor opção sempre será encomendar um transformador (cerca de 12Volts – 150A regime pulsante) do que fazer a gambiarra de se aproveitar o transformador de um micro ondas.
Enrolando o enrolamento:
Conforme figuras 12, 13 e 14, tentei várias configurações de enrolamento.
- Figura 12 – 25mm2 com isolamento de PVC, que consegui 2,1V a 5,5A
- Figura 13 – 10mm2 com isolamento de PVC, que consegui 5,3V a 8,0A
- Figura 14 – 2mm2 esmaltado, que consegui 53V, que derrubou o disjuntor da casa.
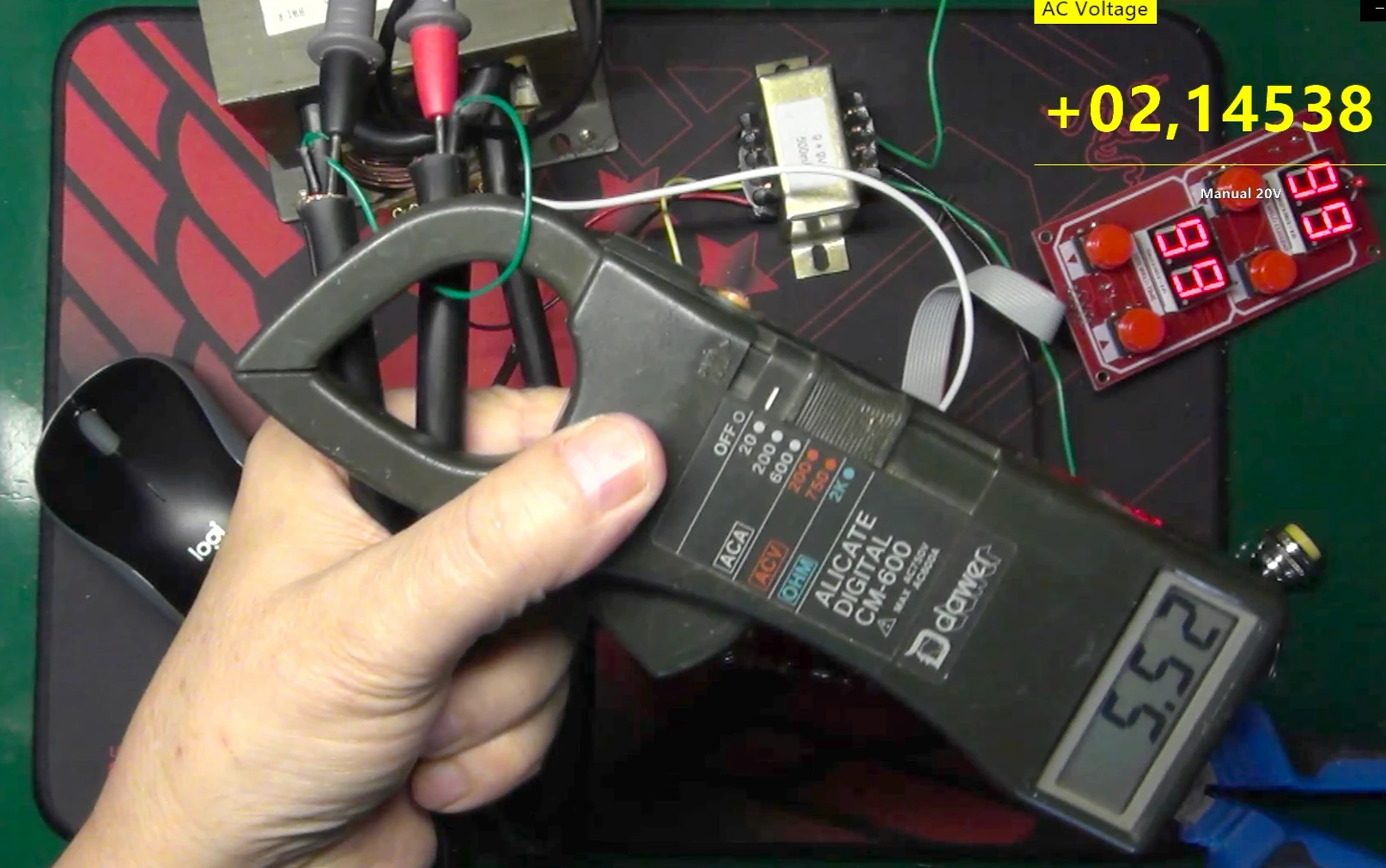
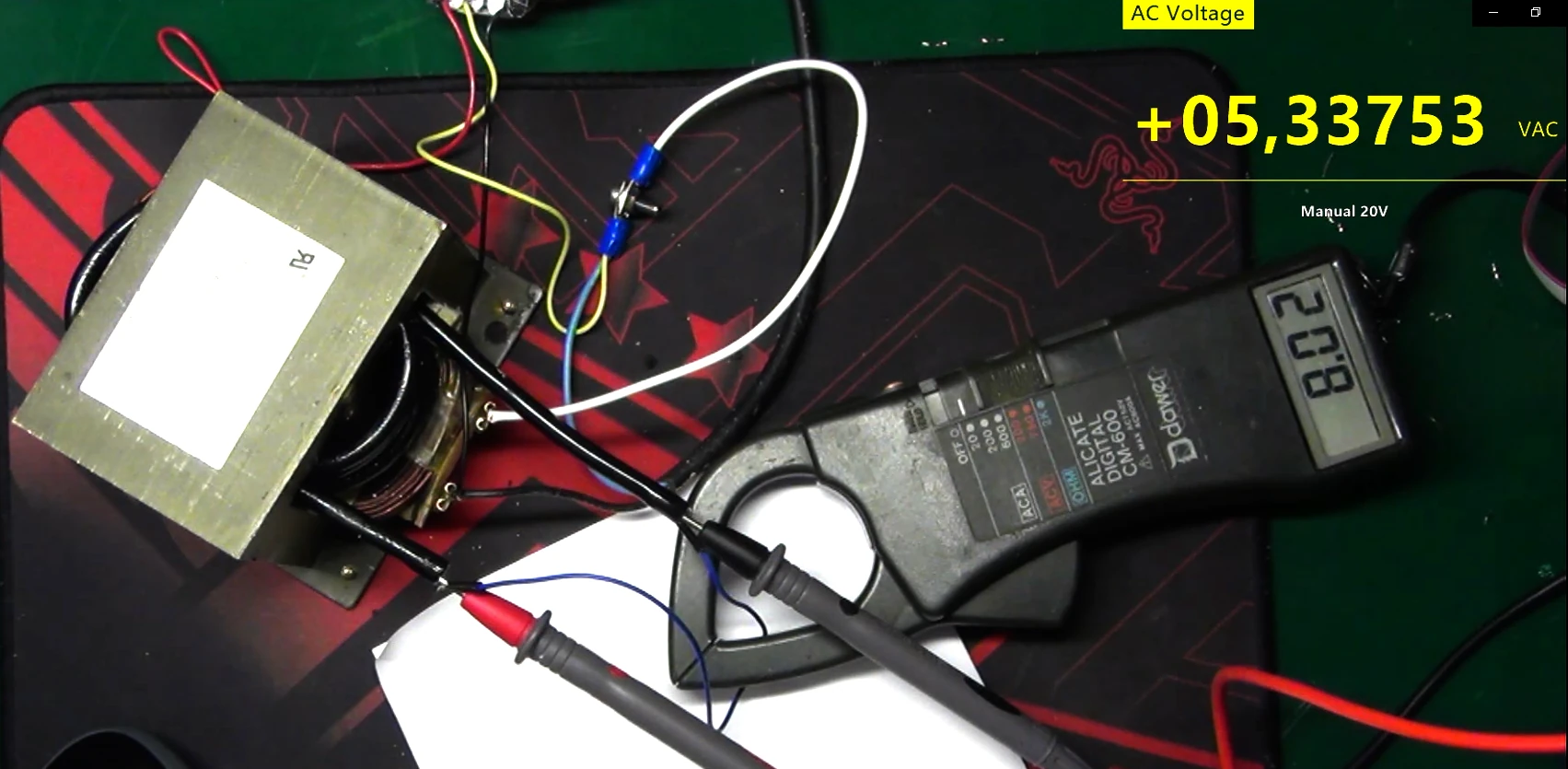
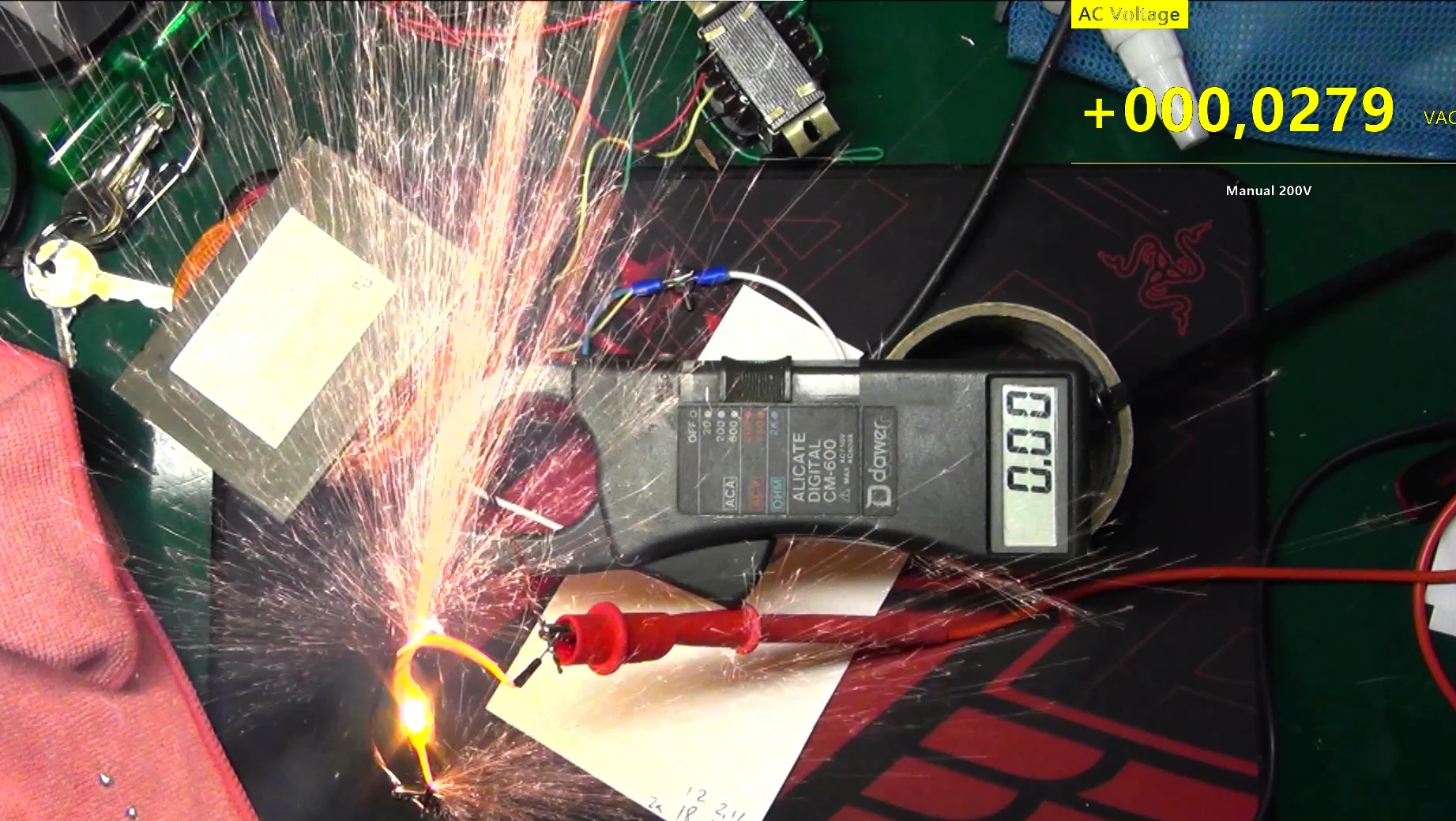
Nenhuma das opções acima funcionaram satisfatoriamente.
Pesquisando um pouco mais:
Percebi que a espessura do isolante estava influenciando no funcionamento do transformador. Nos testes com cabo de bitola maior (25mm2), estava dando pouca corrente, quando deveria dar muito mais corrente se comparado aos demais testes.
Isso é óbvio: O fluxo magnético prefere passar no núcleo do transformador e ou através do enrolamento. O fluxo magnético “não gosta” de passar pelo isolante da fiação e ou pelo ar. Por isso eu estava conseguindo baixas correntes nos testes das figuras 12 e 13.
Observando a figura 14, dá para ver que certamente consegui muito mais corrente, quando utilizei fio esmaltado, porém a bitola do fio e a tensão obtida eram inadequadas. Foi um teste mais para ver o circo pegando fogo mesmo :-).
Resolvendo o problema do enrolamento:
Depois daqueles testes, peguei dois metros de cabo 21mm2 extra flexível para bateria, removi a capa protetora do mesmo e a substitui por espaguete termo retrátil.
Na figura 15 abaixo podemos ver a capa original do cabo. Dá para ver que ela tem uma parede bem espessa.
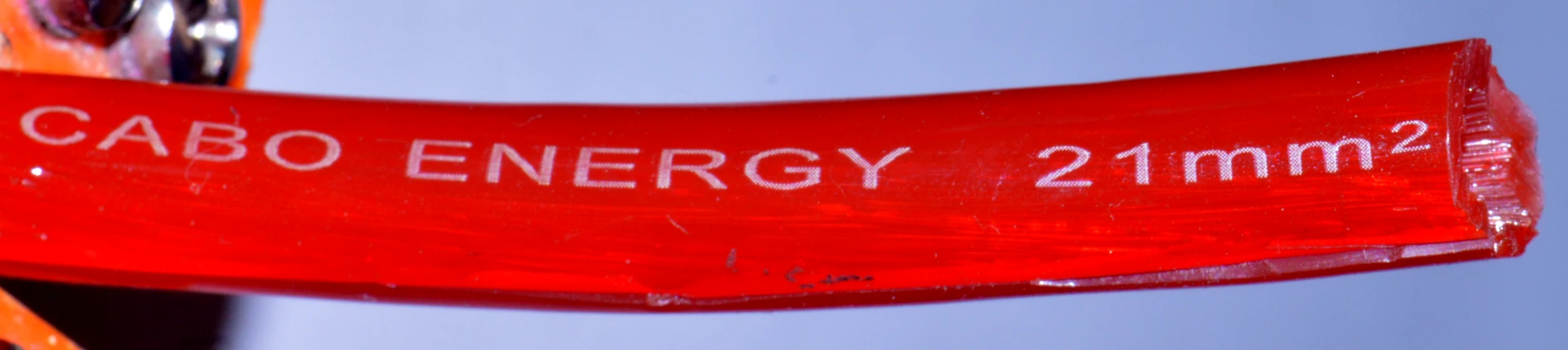
Na figura 16 abaixo, podemos ver o espaguete termo retrátil, já colocado como isolante do cabo de 21mm2 extra flexível.
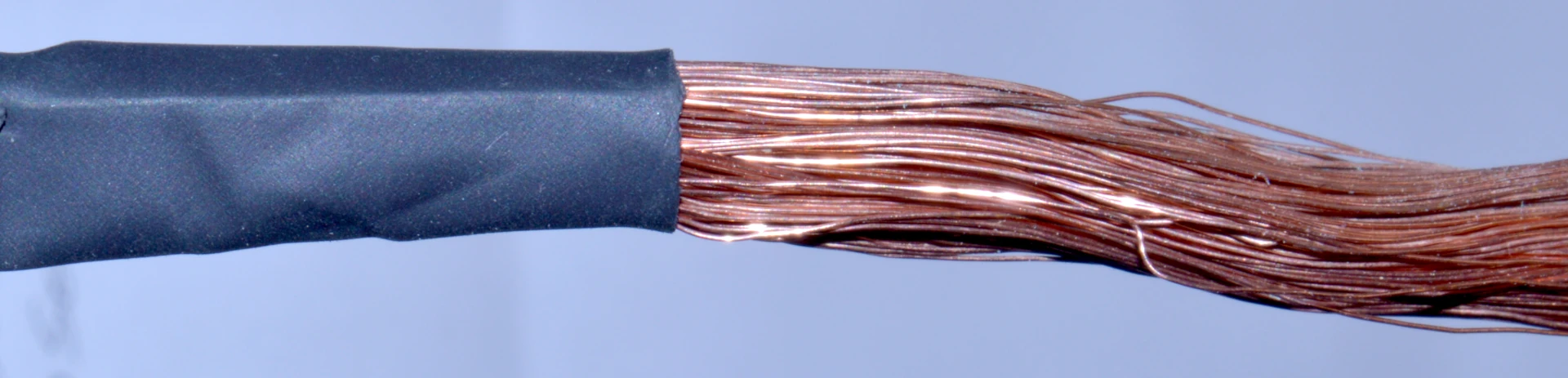
A partir dessa simples mudança de se utilizar o espaguete como isolante, foi diminuída significativamente a quantidade de material isolante, aumentando a proximidade dos fios entre si e entre os fios e o corpo do transformador.
Como os fios estão livres dentro do espaguete, eles também tem a possibilidade de se acomodarem conforme o necessário, conseguindo ocupar todo o núcleo do transformador com muito mais facilidade, conforme podemos ver na figura 17 abaixo, mostrando o enrolamento final, com 6 voltas no transformador.
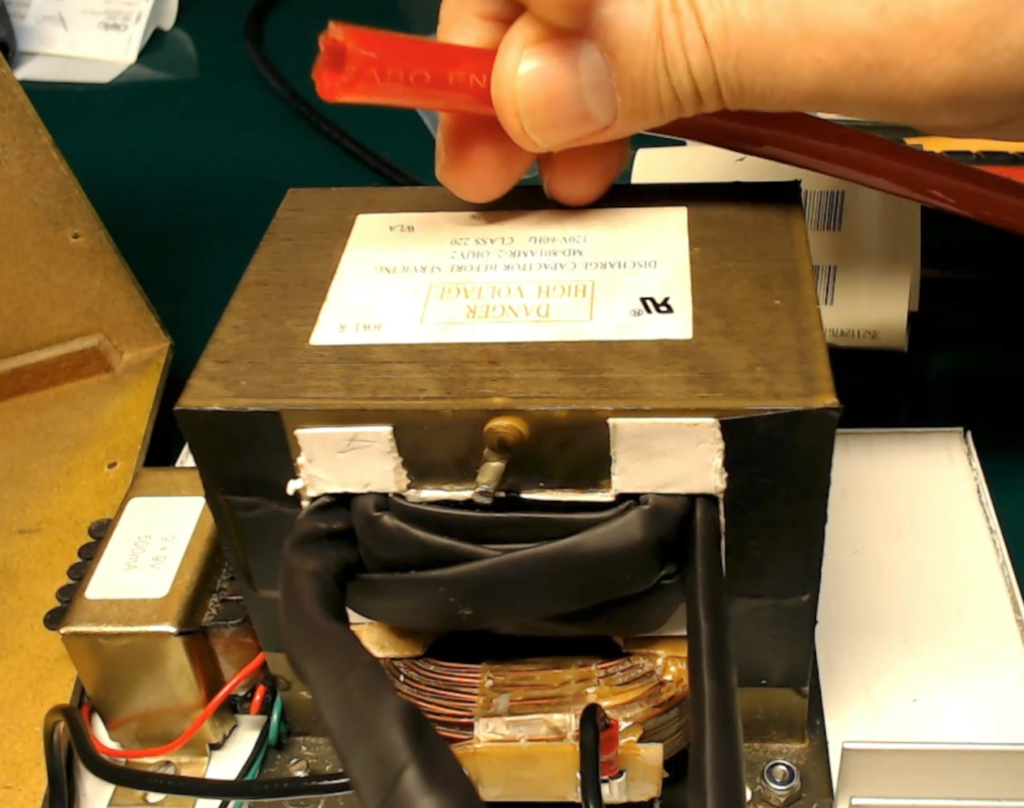
Finalizando:
A minha preocupação nesse artigo foi elencar algumas dificuldades que encontrei enquanto montando o aparelho de solda a ponto a partir do transformador de micro ondas.
O legal desse artigo é que tem uma série de dicas sobre montagens de equipamentos, como fazer dobras, espaçadores e como furar alumínio entre outras, cabendo ao leitor correr atrás de maiores detalhes.
Quanto a montagem em si, na minha opinião não vale a pena montar um e aparelho de solda a ponto utilizando transformador de micro ondas para soldar baterias a menos que todos os componentes venham do aproveitamento de materiais de sucata, fora que na minha opinião, o aparelho tem pouca potência para fazer o serviço direito.
Se tiver a sucatinha ali disponível, faça. Caso contrário compre um novo.

Acima, na figura 18, tem o aparelho final. Note que o cabo é bem mais grosso (21mm2) e ele tem até uma alça para transporte.
Um grande abraço e até o próximo artigo.
Publicado por Renato de Pierri em 23/12/2021